Rotational molding is a manufacturing process that has been in existence for over a century and is commonly practiced in industries such as automotive, sports equipment, and furniture. It’s a process that involves heating and rotating hollow molds to produce seamless and high-quality plastic products. In this blog, we’ll take a comprehensive look at Plastics Rotational Molding, how it works, materials used, advantages, and applications.
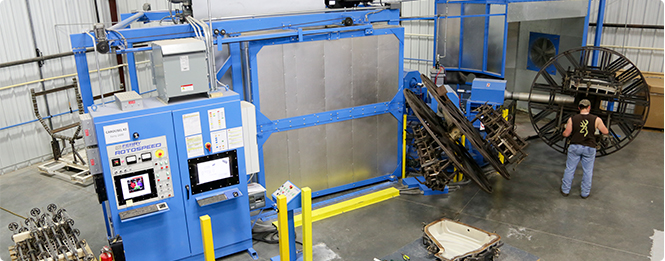
Rotational Molding: How It Works
The rotational molding process is based on a simple principle of using heat and rotation to produce hollow plastic products. It involves heating a mold to a specified temperature, inserting a specified amount of plastic materials, and rotating the mold on different axes while heating uniformly to ensure that the material melts evenly. This ensures that the material coats and forms a solid layer on the inside surface of the mold. Once it cools and solidifies, the mold is removed, and the completed product is left behind.
Types of Materials Used in Rotational Molding
Several materials can be used in rotational molding, including polyethylene, PVC, nylon, and polypropylene. The most commonly used material is polyethylene because it’s flexible, durable, and has excellent chemical resistance. HDPE (high-density polyethylene) is often used in the production of fuel tanks, kayaks, and containers. PVC (polyvinyl chloride) is used in the production of plastic bottles, containers, and pipes. Nylon is used in producing gears, bearings, and auto parts.
Advantages of Rotational Molding
One of the most significant advantages of rotational molding is its ability to produce high-quality, seamless plastic products that are strong, durable, and resistant to chemicals. Other advantages include the ability to produce complex shapes and designs, high production outputs, and low costs per component compared to other plastic molding methods.
Applications of Rotational Molding
Rotational molding has a wide range of applications in different industries. The automotive industry uses it to produce fuel tanks and other car parts while the outdoor sports industry uses it to produce kayaks, helmets, and footballs. The medical industry uses rotational molding to produce surgical instruments and other medical equipment. It also finds use in producing furniture, plastic bins, toys, and agricultural equipment.
Rotational molding is a versatile manufacturing process used to produce a wide range of high-quality plastic products. It’s a low-cost, high-production output method that produces seamless designs while maintaining high durability and chemical resistance. From automotive parts to home supplies, rotational molding has a wide range of applications and is an essential process in modern manufacturing. Now that you know the incredible benefits of rotational molding, you can make an informed decision about using it for your next project.
With the right provider and expert advice, you can produce high-quality products that will exceed your expectations. Contact a rotational molding expert to learn more about how this process can help you create the perfect product for your needs. With rotational molding, you can create products that are not only strong and durable but also beautiful and unique. Let an experienced provider help you bring your vision to life today!